DEGAS SYSTEMS
Altay Dox Ultra-High Efficiency DI Water and Chmistry Degas Unit
Benefits of Degassed DI water with low Dissolved Oxygen (DO)
• For semiconductor wafer processing applications requiring “oxide free” surface preparation:
* minimizes the initial surface oxide density level and provides a more stable H-terminated surface vs. queue time as the DO is reduced (queue time is the exposure time of the “oxide free” wafers to air between the oxide removal process and their placement into an inert environment)
* prevents surface roughening, faceting and undesired silicon removal
* prevents surface water marks & particles generated from silica formation
* provides ultra-pure SiO2 chemical passivation when used for mixing with O3 gas for a DIO3 rinse (1-20 ppm) following an HF last process
• Prevents bacterial growth
• Prevents corrosion
Understanding Oxide Thickness, Monolayers (ml) and AOD for Surface Termination Capability Assume the silicon wafer surface is terminated with either SiOx or SiHx species
Critical factors to optimize a pristine, “oxide free” and H-terminated wafer surface (ex. Si, SiGe, Ge)
• Minimize the impurity concentrations to < 1ppb (ppt) in all of the chemicals (ex. DI water, HF, HCl, IPA and N2) and materials
used for the wet process equipment’s process vessel, plumbing and components.
• Minimize the exposure of the process chemistry and wafers to ambient air, namely O2, H2O (moisture) and organics, during and after the oxide removal process.
• Minimize permeation of O2, CO2, N2 etc. into the process chemistry using proper materials in the process equipment, inert gas
purging above the process vessel, and chemical conditioning.
* While it is impossible to measure absolute “oxide free” this term is used to describe below the detection limits of ultra-sensitive and widely accepted surface characterization methods like SIMS and ESCA (XPS)
Why is degassing the DI water the most important factor to “oxide free” wafer surface preparation?
The optimized process chemistry for the native oxide removal (typically dHF and/or dHCl) uses > 95% DI water during the
oxide removal mixture fill, etch and rinse steps
• Undegassed DI water typically contains ~2-7 PPM levels of dissolved oxygen and other undesirable gases/impurities.
• The post-oxide etch surface oxygen dose (at/cm^2) is directly related to the DO.
• The effect of optimizing the etching chemistry, process recipe, plumbing materials and permeation prevention are all very
important, but the DI water (and chemical) degassing have the largest impact on the “oxide free” surface integrity.
• Membrane contactor technology (using the vacuum + N2 sweep mode) is the most efficient (> 99.999%), safe and costeffective
means to degas DI water and chemicals.
Understanding Oxide Thickness, Monolayers (ml) and AOD for Surface Termination Capability
Assume the silicon wafer surface is terminated with either SiOx or SiHx species
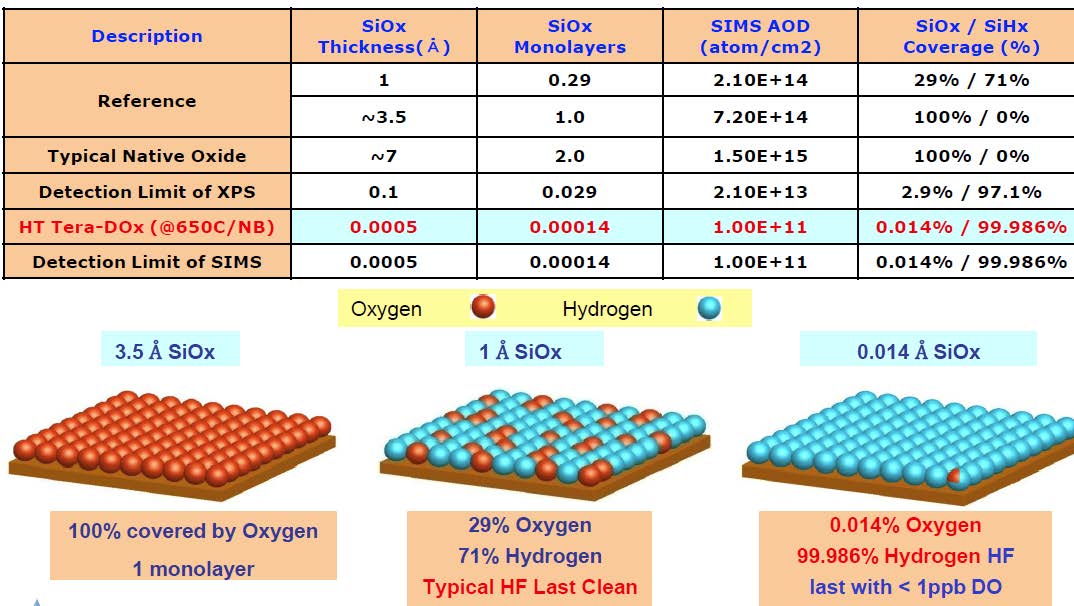